Dominion Energy, headquartered in Richmond, Virginia, is among the nation’s largest producers and transporters of energy. To help power its communities, Dominion Energy employs 16,200 people to operate its massive electric and gas generation system.
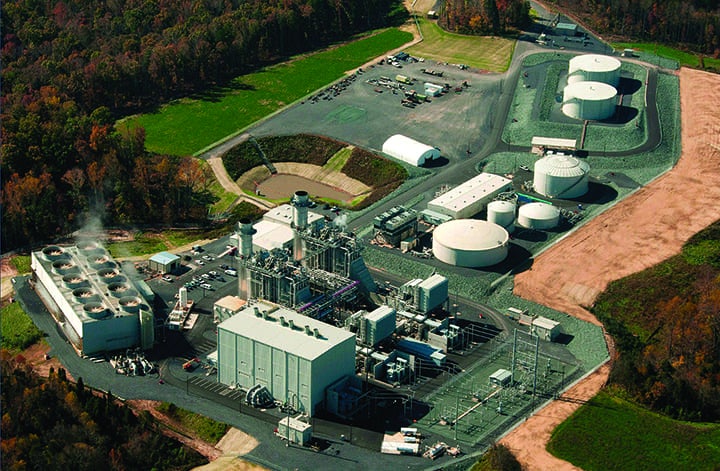 |
1. The Bear Garden Power Station in Virginia is a 590-MW natural gas-fired facility that began commercial operation in May 2011. The plant has a two-on-one configuration, with two combustion turbines generating electricity. Exhaust heat from the turbines produces steam, which is used to generate more electricity. Fluor provided engineering, procurement, construction, and commissioning services for the plant. Courtesy: Fluor
|
Dominion’s Bear Garden Power Station (Figure 1), a 590-MW natural gas-fired facility located in Buckingham County, Virginia, is responsible for powering 146,000 homes in the area. The station’s control room is staffed by a team of operators who work 12-hour shifts to ensure the station runs safely and effectively.
These strenuous shifts hinge on a sharp attention to detail. As such, the control room at the station needs to reflect an environment where employees can safely and comfortably perform their duties.
“I had been pushing for a control room console upgrade for a while,” said Jay Postak, a former engineer at the Bear Garden Generating Station. “Our primary objective was to provide a healthier environment for our operators.”
A Familiar Partner
When searching for a company to help create a more ergonomic environment for the Bear Garden operators, Postak didn’t have to look far. His manager, having recently upgraded Dominion’s Clover Power Station, an 865-MW coal-fired plant in Clover, Virginia, recommended Winsted. The Minneapolis, Minnesota-based company is a global leader in command and control room consoles, desks, and furniture for 24/7 mission-critical applications. Winsted is known for its range of ergonomic sit/stand continuous use technical desks and furniture to reduce fatigue and promote productivity, while meeting International Organization for Standardization (ISO) and Occupational Safety and Health Administration (OSHA) ergonomic guidelines.
Postak took a look at Winsted and hit the ground running with the company’s Wels software, which allows users to digitally design 3D control rooms with Winsted consoles and furniture. With the software, he could begin to lay out the custom console setup his operators needed.
“It proved useful, helping me get better use of the area we had,” said Postak. “With the room’s dimensions, we were able to re-adjust the console and present multiple options to the operators for their feedback.”
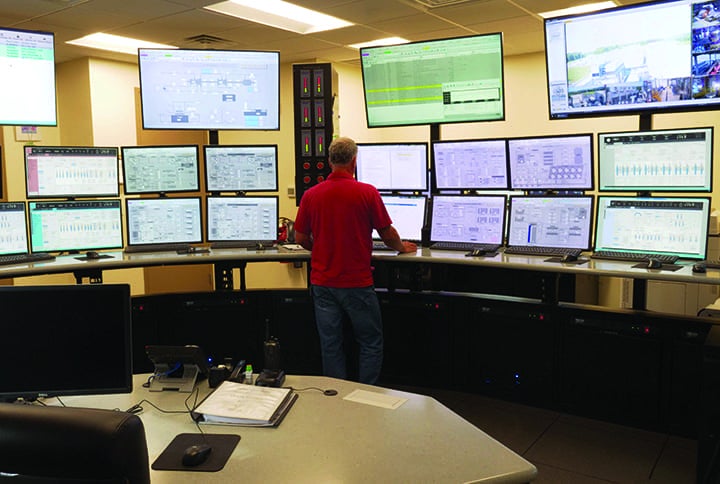 |
2. The upgraded control room at the Bear Garden Power Station in Virginia features 24 display monitors. The layout was configured using Winsted’s Wels software, which allows users to digitally design 3D control rooms, allowing for a customized setup. Courtesy: Winsted
|
Once the design was finalized, Postak engaged Winsted to find the right products for the layout. To give the operator a full view of the two windows in the control room, a large L-shaped desk was placed in the center of the room. This allows for easy access to the front and back of the console, including the cables for the 24 displays (Figure 2).
The entire L-shaped design was configured to allow operators to sit or stand as well. Driven by six servo motors, the entire work surface can be raised to a height of 43 inches. A supervisor station oversees the activity of the main desk, and an engineer’s work station was placed at the far end of the room to allow operators and engineers to work in close proximity with each other.
Postak referenced features of the Clover Power Station when deciding on the configuration of the console, mainly highlighting ergonomics and comfort. “My main priority was making the work surface comfortable for the operators,” he said. “I learned the Clover station had inset monitors, which is more practical for long-time viewing.”
Ideal Installation
Success hinged on smooth installation, and this particular project provided its own set of challenges. The amount of equipment being installed, and the large L-shaped console, required a hands-on approach.
Winsted staff arrived onsite for the install. The L-shaped console was delivered in three sections. To secure everything in place, Winsted super-glued blocks onto the sections, and also placed glue in the cracks between the sections. A next step was using C-clamps to anchor everything together. Once the glue dried, the installation team returned to remove the blocks and buffed the entire surface, resulting in one continuous surface.
“I was wondering what it was going to look like when it was done,” said Postak. “In the end, you couldn’t tell. There were no seams.”
To ensure that Bear Garden’s budgetary requirements were met, Winsted worked to fulfill the product order, and the installation was completed in a couple months. “I didn’t sign off on the final design drawings until the middle of November,” said Postak. “They started construction and everything was onsite by the end of December.”
During the process, Winsted and Postak were able to quickly navigate an issue regarding the desk height, leading to no loss in construction time. This was primarily due to the use of the 3D computer-aided design image of the console that was produced by the Winsted designer.
Success at Bear Garden
With the new ergonomically designed console at Bear Garden, the operators have a work area that fits their 12-hour work schedule. Despite the large scale of the project and installation, creating this ergonomic environment was a smooth undertaking.
“It was really remarkable,” said Postak. “Winsted was very accommodating, and we have a great control room as a result.” ■
—Randy Smith is president and general manager of Winsted, a provider of command and control room consoles, desks, and furniture for 24/7 mission-critical applications.
yeezy comments at 2023-04-09 02:29:17
I precisely needed to appreciate you once again. I'm not certain what I would have implemented in the absence of the actual suggestions shown by you concerning such industry. It seemed to be a very fearsome situation for me, nevertheless discovering this expert way you managed that took me to cry over contentment. Extremely happy for this work and thus hope that you find out what a powerful job that you're getting into educating many people by way of your website. Most likely you have never met all of us.
[url=http://www.adidasyeezyuk.com]yeezy[/url]
golden goose superstar sneakers comments at 2023-04-09 03:04:11
I抎 need to test with you here. Which is not something I normally do! I take pleasure in studying a submit that will make individuals think. Additionally, thanks for permitting me to comment!
golden goose superstar sneakers
yeezy comments at 2023-04-09 22:35:26
I happen to be commenting to let you be aware of what a impressive discovery our child obtained using your webblog. She picked up many things, most notably what it's like to possess an incredible coaching spirit to get folks without difficulty gain knowledge of a variety of very confusing topics. You actually surpassed her expectations. Many thanks for displaying those important, safe, educational not to mention fun tips on that topic to Janet.
yeezy
off white clothing outlet comments at 2023-04-10 18:53:50
I wish to express thanks to you for rescuing me from such a situation. Right after browsing through the search engines and meeting things that were not pleasant, I was thinking my life was well over. Existing without the presence of strategies to the problems you've resolved as a result of your entire article is a serious case, as well as the kind that could have negatively affected my career if I hadn't discovered your web site. Your primary expertise and kindness in maneuvering all the things was vital. I am not sure what I would have done if I hadn't come upon such a point like this. I'm able to now relish my future. Thanks for your time very much for this reliable and effective help. I will not think twice to suggest your site to anyone who should have guide about this subject.
off white clothing outlet
bape clothing comments at 2023-04-11 13:36:48
Thanks a lot for giving everyone such a pleasant chance to read from this web site. It's always very enjoyable and full of amusement for me and my office peers to search your web site more than three times every week to study the new items you have. Of course, I'm just always contented with the wonderful suggestions served by you. Certain two tips in this posting are essentially the best I have ever had.
bape clothing
off white outlet comments at 2023-04-12 08:45:57
I intended to send you the little bit of word to say thank you as before for your personal pretty secrets you've discussed on this page. It's certainly shockingly generous of people like you to convey extensively precisely what many of us could have made available as an electronic book to make some money for themselves, specifically since you might well have done it in the event you decided. These smart ideas also acted as the easy way to understand that many people have the same interest much like my very own to figure out way more related to this problem. I believe there are a lot more fun occasions in the future for people who looked over your site.
off white outlet
kd13 comments at 2023-04-13 04:49:00
My husband and i got absolutely thrilled Raymond managed to carry out his research out of the precious recommendations he grabbed out of your site. It is now and again perplexing to simply find yourself giving out facts which men and women might have been trying to sell. So we understand we now have you to be grateful to for that. All of the explanations you made, the straightforward web site navigation, the relationships you assist to foster - it's mostly extraordinary, and it is leading our son and our family imagine that this topic is cool, and that is extraordinarily important. Thanks for the whole lot!
kd13
supreme new york comments at 2023-04-14 00:39:57
I have to show some appreciation to you just for bailing me out of this setting. Because of researching throughout the online world and meeting proposals that were not productive, I was thinking my entire life was over. Existing without the presence of answers to the difficulties you've solved as a result of your good article is a serious case, and ones that could have in a negative way affected my entire career if I had not discovered the website. The talents and kindness in controlling almost everything was crucial. I'm not sure what I would've done if I hadn't come across such a point like this. I can also at this time look forward to my future. Thanks so much for this specialized and result oriented guide. I will not think twice to propose your web site to any individual who will need counselling about this situation.
supreme new york
golden goose mid star comments at 2023-04-14 02:58:13
Can I simply say what a aid to seek out someone who really knows what theyre speaking about on the internet. You undoubtedly know easy methods to convey an issue to light and make it important. Extra folks must learn this and perceive this aspect of the story. I cant believe youre no more standard because you undoubtedly have the gift.
golden goose mid star
off white jordan 1 comments at 2023-04-14 21:21:28
A lot of thanks for all of the efforts on this web site. My mum take interest in conducting investigations and it's really easy to understand why. We hear all concerning the powerful manner you render worthwhile ideas through the blog and as well as recommend response from other ones on this content so our own princess is now studying a great deal. Enjoy the rest of the new year. You're doing a splendid job.
off white jordan 1
supreme comments at 2023-04-15 17:54:27
I have to voice my affection for your kindness giving support to individuals who must have assistance with the subject. Your very own commitment to passing the message around has been really functional and has continually enabled individuals much like me to attain their aims. Your entire warm and helpful guideline can mean a great deal to me and especially to my mates. Thanks a lot; from each one of us.
supreme
golden goose purestar comments at 2023-04-17 00:13:29
I抎 need to examine with you here. Which isn't something I usually do! I get pleasure from studying a post that may make people think. Also, thanks for allowing me to remark!
golden goose purestar
hermes handbags comments at 2023-04-17 09:08:22
Thanks a lot for providing individuals with remarkably splendid chance to read articles and blog posts from this web site. It really is so good and packed with a good time for me personally and my office co-workers to search the blog no less than three times in 7 days to read through the latest things you have got. And definitely, we're always pleased with your impressive suggestions you serve. Some 4 tips in this posting are certainly the most suitable we have all had.
hermes handbags
yeezy wave runner 700 comments at 2023-04-18 04:30:01
A lot of thanks for all your hard work on this site. Debby enjoys participating in research and it is obvious why. My spouse and i learn all concerning the lively form you produce worthwhile secrets via this blog and even inspire response from the others about this theme plus my princess is actually studying a whole lot. Take pleasure in the remaining portion of the year. You have been carrying out a powerful job.
yeezy wave runner 700
stephen curry shoes comments at 2023-04-18 23:51:05
I'm just commenting to make you understand of the impressive encounter our princess encountered going through your webblog. She mastered numerous things, with the inclusion of how it is like to possess an excellent teaching heart to have other individuals completely know just exactly some specialized subject areas. You truly exceeded our desires. I appreciate you for offering such useful, dependable, revealing and also unique tips on the topic to Evelyn.
stephen curry shoes
yeezy boost 350 comments at 2023-04-19 19:41:30
I in addition to my pals appeared to be viewing the good guides found on your web page then at once developed an awful suspicion I had not expressed respect to the website owner for those tips. The guys happened to be consequently thrilled to read them and have honestly been loving these things. We appreciate you being really kind as well as for picking out such great resources most people are really desirous to understand about. Our own honest regret for not expressing appreciation to you sooner.
yeezy boost 350
golden goose hi star comments at 2023-04-19 20:56:40
You must participate in a contest for among the finest blogs on the web. I will suggest this site!
golden goose hi star
kyrie shoes comments at 2023-04-20 09:58:07
I simply had to thank you so much once again. I'm not certain the things I could possibly have undertaken in the absence of these opinions provided by you on such a concern. This has been a frustrating issue in my circumstances, nevertheless understanding the well-written avenue you dealt with the issue made me to weep with fulfillment. Extremely happy for your information and as well , trust you know what an amazing job that you are putting in teaching the mediocre ones thru your web page. I am certain you have never come across any of us.
kyrie shoes
yeezy comments at 2023-04-23 00:49:58
Thanks for all of your labor on this site. My aunt delights in managing internet research and it's really simple to grasp why. Most of us notice all regarding the compelling tactic you make reliable tactics by means of the blog and even foster response from the others on the content while our favorite simple princess is learning so much. Have fun with the remaining portion of the year. You have been doing a pretty cool job.
yeezy
kd 12 shoes comments at 2023-04-23 16:03:13
I must voice my gratitude for your kindness giving support to those people that have the need for help on this important content. Your very own commitment to passing the solution all over became pretty productive and has continually encouraged associates like me to reach their dreams. The interesting hints and tips means a lot to me and far more to my fellow workers. Many thanks; from all of us.
kd 12 shoes
golden goose dad star comments at 2023-04-24 02:12:41
I'm typically to running a blog and i actually admire your content. The article has really peaks my interest. I'm going to bookmark your web site and keep checking for brand new information.
golden goose dad star
supreme outlet comments at 2023-04-24 07:06:24
My wife and i got so excited Ervin managed to complete his preliminary research through your precious recommendations he obtained through your weblog. It is now and again perplexing to just be releasing guidelines some other people have been trying to sell. And we do know we now have the website owner to be grateful to for that. The most important illustrations you've made, the easy site menu, the relationships your site give support to foster - it's many impressive, and it is aiding our son in addition to the family reckon that that concept is enjoyable, and that is particularly essential. Thanks for the whole lot!
supreme outlet
off white shoes comments at 2023-04-24 22:29:38
My spouse and i were now happy when Louis could complete his analysis through the precious recommendations he received in your web site. It is now and again perplexing to simply possibly be offering secrets and techniques some people might have been selling. So we already know we have got the website owner to be grateful to because of that. Most of the explanations you have made, the easy web site menu, the friendships you can assist to foster - it's got all fabulous, and it's aiding our son in addition to our family feel that this situation is awesome, and that's really essential. Thanks for the whole thing!
off white shoes
bapesta shoes comments at 2023-04-25 13:23:45
I simply wanted to say thanks once again. I do not know what I would've used without the actual smart ideas discussed by you regarding my question. It actually was an absolute horrifying concern in my circumstances, nevertheless noticing the very professional technique you treated the issue forced me to leap with delight. I am just happier for your help as well as expect you recognize what a great job you're getting into training other individuals through your websites. I'm certain you've never encountered any of us.
bapesta shoes
hermes birkin comments at 2023-04-26 04:42:28
I not to mention my pals were actually going through the excellent items located on your site and so before long I had a terrible suspicion I had not expressed respect to the web blog owner for those techniques. Those ladies appeared to be glad to study all of them and now have seriously been using them. We appreciate you being very helpful and then for settling on this form of fine issues most people are really desirous to understand about. My very own honest regret for not expressing gratitude to sooner.
hermes birkin
golden goose sabot comments at 2023-04-26 06:26:38
Whats up! I simply wish to give an enormous thumbs up for the great data you could have right here on this post. I will likely be coming again to your blog for extra soon.
golden goose sabot
kd 14 comments at 2023-04-28 02:19:10
My wife and i were really fulfilled that Michael could complete his preliminary research out of the ideas he made in your weblog. It is now and again perplexing to just be giving out information and facts other folks may have been making money from. We really understand we have you to give thanks to for that. All of the explanations you've made, the straightforward site navigation, the friendships you make it possible to create - it's most powerful, and it's facilitating our son and the family reason why that concept is brilliant, which is pretty mandatory. Thanks for all!
kd 14
supreme new york comments at 2023-04-28 18:02:17
I needed to send you that very small word so as to give thanks once again relating to the precious things you have featured above. It's pretty generous with you in giving unreservedly just what most of us might have offered as an e book in order to make some cash on their own, most notably now that you could possibly have tried it in the event you desired. These inspiring ideas as well served to be the fantastic way to fully grasp that other people online have a similar zeal the same as my personal own to find out whole lot more concerning this matter. I believe there are thousands of more fun opportunities up front for folks who see your website.
supreme new york
off white comments at 2023-04-29 09:44:29
I simply desired to say thanks once again. I am not sure what I would've undertaken in the absence of those solutions shared by you concerning my topic. It previously was a intimidating issue in my opinion, but taking a look at the very specialised manner you solved that took me to cry for gladness. Now i am thankful for the help as well as believe you realize what a great job you are always providing training most people through the use of a web site. More than likely you haven't got to know any of us.
off white
bape clothing outlet comments at 2023-04-30 16:38:09
Thanks for all your valuable work on this blog. Debby delights in managing internet research and it is simple to grasp why. All of us hear all relating to the dynamic tactic you offer effective tactics on your web site and therefore encourage participation from other individuals on the subject and our own girl is starting to learn a whole lot. Enjoy the remaining portion of the new year. You have been carrying out a useful job.
bape clothing outlet
golden goose sneakers comments at 2023-04-30 16:41:35
Can I just say what a reduction to find someone who actually is aware of what theyre talking about on the internet. You definitely know the way to carry a difficulty to gentle and make it important. Extra people have to read this and understand this facet of the story. I cant consider youre no more well-liked because you undoubtedly have the gift.
golden goose sneakers
golden goose comments at 2023-05-02 08:50:02
I not to mention my guys ended up analyzing the great things found on your web page and then all of a sudden developed an awful feeling I had not expressed respect to the web blog owner for those secrets. The women had been as a result joyful to read through them and have now quite simply been taking pleasure in those things. Thank you for genuinely well thoughtful and also for making a decision on certain wonderful topics millions of individuals are really desperate to be aware of. Our own sincere regret for not expressing gratitude to earlier.
golden goose
air jordan travis scott comments at 2023-05-02 22:39:39
I simply had to appreciate you once more. I am not sure what I would have sorted out without the type of aspects revealed by you directly on that problem. It previously was a real daunting condition for me, but encountering your well-written fashion you resolved that forced me to cry over joy. I will be happy for your service and then believe you find out what a powerful job you're doing training most people through your blog. I'm certain you've never encountered any of us.
air jordan travis scott
off white outlet comments at 2023-05-03 12:16:46
I simply wanted to send a quick word to appreciate you for the precious tips and hints you are showing at this site. My prolonged internet search has finally been honored with good quality details to share with my friends and classmates. I 'd suppose that many of us readers are extremely blessed to live in a decent network with many awesome people with good basics. I feel quite happy to have seen your website page and look forward to tons of more enjoyable minutes reading here. Thank you once again for everything.
off white outlet
golden goose dad star comments at 2023-05-04 14:46:30
Aw, this was a very nice post. In concept I wish to put in writing like this additionally ?taking time and actual effort to make an excellent article?but what can I say?I procrastinate alot and under no circumstances appear to get one thing done.
golden goose dad star
jordan 1 comments at 2023-05-04 16:15:25
I simply wanted to construct a small comment to express gratitude to you for the amazing pointers you are giving on this site. My rather long internet search has now been paid with brilliant facts to go over with my friends and family. I 'd repeat that we website visitors are quite endowed to live in a perfect site with many marvellous individuals with great tips. I feel quite happy to have used your weblog and look forward to really more amazing moments reading here. Thanks a lot once more for everything.
jordan 1
jordan retro comments at 2023-05-05 05:29:00
My husband and i were absolutely fulfilled that Jordan managed to do his preliminary research through your ideas he acquired from your web pages. It's not at all simplistic just to always be giving for free tips and hints that many the rest might have been selling. And we all do know we need the blog owner to appreciate for this. The illustrations you have made, the simple blog navigation, the friendships you can aid to create - it is many unbelievable, and it's leading our son and our family reckon that that matter is pleasurable, which is certainly extremely vital. Thanks for all the pieces!
jordan retro
off white t shirt comments at 2023-05-05 19:54:54
My wife and i ended up being very comfortable Raymond could deal with his analysis using the precious recommendations he had in your blog. It is now and again perplexing to simply continually be making a gift of information and facts people have been trying to sell. Therefore we do understand we need the writer to be grateful to for this. The most important illustrations you made, the straightforward site navigation, the relationships your site assist to instill - it's most astounding, and it is assisting our son in addition to our family reckon that that subject is satisfying, and that is particularly indispensable. Thank you for everything!
off white t shirt
hermes outlet online comments at 2023-05-06 09:15:26
Thanks a lot for giving everyone an exceptionally superb chance to read critical reviews from this website. It's usually so amazing and as well , full of a great time for me and my office peers to visit your web site at a minimum thrice in one week to see the fresh items you will have. And lastly, I'm also at all times satisfied with the terrific tricks you give. Selected 3 facts in this article are rather the most effective I have had.
hermes outlet online
golden goose running sneakers comments at 2023-05-06 17:21:43
you may have an excellent blog here! would you wish to make some invite posts on my weblog?
golden goose running sneakers
jordan shoes comments at 2023-05-06 23:16:59
Needed to write you one little bit of word in order to give thanks once again on the gorgeous basics you have discussed in this case. It has been simply strangely open-handed of you to deliver openly all a lot of folks could have offered for sale for an ebook in order to make some dough for their own end, chiefly considering the fact that you might well have tried it in the event you wanted. These concepts additionally worked to provide a great way to understand that many people have a similar keenness much like my very own to realize more on the topic of this condition. I am sure there are numerous more pleasant times ahead for individuals who scan your blog post.
jordan shoes
OFF-White comments at 2023-05-07 12:59:11
I wanted to create you that tiny word to give thanks once again about the marvelous views you have documented on this page. This is really extremely open-handed with people like you to supply unreservedly precisely what a lot of people could possibly have sold as an e-book to help with making some money on their own, principally seeing that you could possibly have done it if you considered necessary. Those concepts in addition served to be the easy way to fully grasp many people have the identical keenness just as my own to understand significantly more regarding this issue. I believe there are numerous more pleasurable opportunities in the future for people who read your blog post.
OFF-White
jordan shoes comments at 2023-05-08 02:43:50
A lot of thanks for all your valuable labor on this blog. Debby delights in making time for investigation and it's really easy to see why. Most people learn all of the dynamic form you convey functional things through the website and even encourage participation from some others on the subject matter then our favorite simple princess is without question studying so much. Take advantage of the remaining portion of the year. You are always carrying out a first class job.
jordan shoes
bape hoodie comments at 2023-05-08 16:26:35
I am just writing to make you understand of the incredible encounter my friend's princess developed browsing your site. She even learned too many issues, not to mention what it's like to possess an excellent helping heart to let many others quite simply learn about chosen impossible subject matter. You undoubtedly did more than her expectations. Thank you for giving such important, dependable, edifying and unique thoughts on the topic to Evelyn.
bape hoodie
jordan shoes comments at 2023-05-09 05:38:23
I and my guys have already been viewing the best items on your web blog then suddenly came up with a terrible feeling I never thanked the web blog owner for those secrets. My young men are already totally joyful to study them and have now quite simply been making the most of those things. Thanks for being well thoughtful as well as for deciding on this sort of terrific subject matter most people are really desperate to know about. My personal sincere regret for not expressing appreciation to you sooner.
jordan shoes
jordan shoes comments at 2023-05-10 09:40:19
My wife and i were now contented that Chris managed to complete his preliminary research out of the ideas he had from your very own weblog. It is now and again perplexing just to continually be freely giving information which usually many others have been selling. We really do understand we have the blog owner to appreciate for that. Most of the explanations you have made, the easy website navigation, the friendships you will make it possible to foster - it is mostly fabulous, and it's letting our son and the family do think the theme is pleasurable, which is unbelievably pressing. Thanks for the whole thing!
jordan shoes
chrome hearts outlet comments at 2023-05-11 03:31:07
Needed to put you a little note to give many thanks as before with your remarkable solutions you've documented in this article. It was really pretty generous of people like you to deliver freely just what a few individuals would've offered as an electronic book to get some dough for their own end, certainly considering that you might have tried it if you decided. These pointers also served to be a easy way to understand that the rest have a similar interest really like my very own to know lots more on the subject of this matter. Certainly there are millions of more fun situations up front for individuals that find out your blog.
chrome hearts outlet
hermes outlet comments at 2023-05-11 10:10:39
This site is mostly a walk-by means of for the entire information you wanted about this and didn抰 know who to ask. Glimpse here, and you抣l positively uncover it.
hermes outlet
jordan 4 comments at 2023-05-11 11:44:05
My spouse and i got really comfortable when John could complete his web research via the precious recommendations he made when using the site. It's not at all simplistic to just happen to be offering facts that many people have been making money from. And we acknowledge we have the writer to be grateful to for that. The entire explanations you've made, the straightforward website navigation, the friendships you will assist to engender - it is most excellent, and it is aiding our son and our family reckon that this situation is amusing, which is really pressing. Many thanks for all the pieces!
jordan 4
kd 14 comments at 2023-05-12 07:51:18
I would like to point out my affection for your generosity giving support to those people who really want assistance with this one field. Your personal commitment to getting the solution all around was exceptionally valuable and has consistently made many people much like me to realize their goals. Your own invaluable help and advice indicates this much a person like me and far more to my mates. Many thanks; from each one of us.
kd 14
kyrie irving shoes comments at 2023-05-14 20:18:10
I precisely wanted to appreciate you all over again. I am not sure the things that I could possibly have sorted out without the suggestions documented by you relating to my subject matter. It had become a very terrifying matter in my position, nevertheless understanding this expert fashion you treated the issue made me to cry for happiness. Extremely thankful for the guidance and thus believe you really know what a powerful job you're accomplishing instructing most people through your web page. Most probably you've never got to know any of us.
kyrie irving shoes
fear of god comments at 2023-05-15 23:02:31
Thanks so much for providing individuals with such a wonderful chance to read from this blog. It is always so superb plus stuffed with a great time for me personally and my office colleagues to search your site particularly three times a week to find out the new things you will have. Of course, I'm so actually impressed for the exceptional creative ideas you serve. Some two areas in this post are in truth the simplest we've had.
fear of god
nike dunks comments at 2023-05-16 23:33:54
I want to show appreciation to this writer for rescuing me from such a predicament. After searching throughout the internet and getting concepts that were not pleasant, I thought my life was well over. Living devoid of the approaches to the problems you've fixed all through the posting is a crucial case, and those which could have negatively damaged my entire career if I hadn't come across your blog. Your expertise and kindness in handling all the things was vital. I am not sure what I would've done if I had not come upon such a thing like this. It's possible to at this point relish my future. Thank you so much for the impressive and effective help. I won't hesitate to refer your web sites to anybody who should have guidelines on this matter.
nike dunks
off white comments at 2023-05-17 06:40:15
I and also my guys were actually studying the excellent helpful hints located on your web page then all of the sudden I got a horrible suspicion I had not expressed respect to you for those tips. The young boys are already totally happy to read all of them and now have very much been loving those things. We appreciate you turning out to be so helpful as well as for settling on this form of terrific guides millions of individuals are really eager to know about. Our own honest regret for not expressing gratitude to you sooner.
off white
palm angels comments at 2023-05-17 23:04:06
I precisely wished to thank you very much all over again. I do not know the things that I would've undertaken without these aspects provided by you regarding such a area. This was a fearsome difficulty in my opinion, but observing the very skilled fashion you processed the issue forced me to leap with happiness. I'm happier for your support as well as hope you really know what an amazing job you have been putting in educating some other people using your blog. I am sure you have never encountered any of us.
palm angels
bape shoes comments at 2023-05-18 22:32:16
Thanks for your own labor on this blog. Debby really likes setting aside time for research and it's obvious why. All of us notice all concerning the powerful way you create very helpful tips and tricks on this website and in addition inspire response from other individuals on the issue so my girl has always been starting to learn a lot. Enjoy the remaining portion of the new year. You're the one doing a remarkable job.
bape shoes
black golden goose comments at 2023-05-18 23:13:22
I wanted to write down a quick comment to appreciate you for all the lovely tricks you are giving out on this site. My extended internet look up has now been rewarded with good information to talk about with my family members. I would mention that many of us readers actually are definitely endowed to live in a very good place with very many special people with valuable secrets. I feel quite lucky to have come across your web pages and look forward to really more fabulous times reading here. Thank you once again for everything.
black golden goose
off white outlet online comments at 2023-05-19 05:37:19
I precisely desired to appreciate you yet again. I am not sure what I would have gone through in the absence of the entire aspects documented by you over my theme. Entirely was a very difficult case for me, but taking a look at a new well-written fashion you processed the issue forced me to weep over contentment. Now i am happy for this help as well as sincerely hope you know what a great job your are providing teaching many people using your web page. Probably you have never met any of us.
off white outlet online
yeezy 350 comments at 2023-05-19 23:13:52
Thanks a lot for giving everyone an extraordinarily breathtaking possiblity to read articles and blog posts from this website. It is often so pleasing and also full of fun for me and my office acquaintances to visit your blog minimum three times per week to read the newest things you have got. And definitely, I am also actually astounded with the special things you give. Selected 1 facts in this post are basically the finest we have all had.
yeezy 350
off white hoodie comments at 2023-05-20 06:23:10
I wanted to put you one very small word to say thanks as before considering the spectacular things you have contributed on this page. It's quite surprisingly open-handed of you to grant freely what exactly a few individuals could have advertised for an electronic book to earn some money for their own end, chiefly now that you might well have done it if you considered necessary. The techniques as well served to be a easy way to be aware that most people have the identical passion like my personal own to know the truth lots more pertaining to this condition. I am certain there are some more fun periods in the future for individuals that looked over your website.
off white hoodie
goyard outlet comments at 2023-05-21 00:11:17
I precisely wanted to thank you so much once again. I am not sure what I might have followed in the absence of these basics discussed by you on such a subject matter. It previously was a real distressing situation in my view, but being able to view your professional mode you solved that forced me to cry with gladness. Extremely happier for this work and as well , wish you recognize what a powerful job that you are undertaking teaching the others with the aid of your blog. Probably you've never come across any of us.
goyard outlet
fear of god outlet comments at 2023-05-21 08:00:14
I am also commenting to make you know of the fabulous discovery my cousin's child had studying your web page. She realized a good number of pieces, which included what it is like to have a wonderful coaching spirit to have other people with no trouble know specific complex matters. You undoubtedly exceeded people's expected results. I appreciate you for showing these useful, trustworthy, explanatory and cool tips on that topic to Jane.
fear of god outlet
paul george shoes comments at 2023-05-22 01:24:41
My wife and i felt absolutely fulfilled Ervin could complete his basic research through your ideas he came across from your very own blog. It is now and again perplexing just to continually be giving for free guides that some others could have been selling. Therefore we take into account we now have the writer to thank for that. All the illustrations you've made, the easy website navigation, the relationships you can give support to engender - it's many overwhelming, and it's really helping our son and our family recognize that this idea is pleasurable, which is certainly especially essential. Many thanks for the whole thing!
paul george shoes
supreme hoodie comments at 2023-05-24 03:07:34
I simply desired to appreciate you again. I do not know the things that I could possibly have worked on without the entire recommendations documented by you regarding that concern. Certainly was a real distressing case for me personally, nevertheless encountering the very specialized fashion you treated it took me to leap over delight. I'm happy for this service and then hope that you find out what a great job you have been getting into educating the mediocre ones thru your websites. Most probably you've never got to know all of us.
supreme hoodie
bape official comments at 2023-05-24 11:17:57
I together with my guys have already been following the good tips and hints on your web page then suddenly came up with an awful feeling I never thanked the web blog owner for those strategies. The young boys appeared to be totally warmed to study them and have now clearly been taking advantage of them. I appreciate you for getting considerably accommodating and also for settling on some notable topics millions of individuals are really needing to know about. My very own sincere regret for not expressing gratitude to sooner.
bape official
goyard comments at 2023-05-25 04:50:41
I enjoy you because of all your valuable effort on this website. Kate delights in carrying out research and it's simple to grasp why. Most people notice all of the powerful mode you deliver helpful information by means of the web blog and therefore invigorate response from other ones on that theme so my simple princess has been learning a lot of things. Enjoy the remaining portion of the new year. You have been performing a remarkable job.
goyard
off white shoes comments at 2023-05-25 13:48:53
I wanted to send you that tiny remark so as to thank you very much the moment again just for the great suggestions you have shared on this website. This has been so surprisingly open-handed of people like you to offer unreservedly what exactly many of us could have offered as an electronic book to earn some profit for their own end, notably now that you could possibly have done it if you ever decided. The basics in addition served like a great way to comprehend other individuals have similar fervor much like my own to realize great deal more regarding this matter. I know there are many more pleasant instances in the future for individuals that examine your site.
off white shoes
Jordan Travis Scott comments at 2023-05-27 09:15:49
I want to voice my respect for your kind-heartedness supporting people who should have assistance with that concept. Your very own commitment to getting the solution all around appeared to be extremely useful and has truly enabled folks just like me to arrive at their goals. Your own informative key points implies a lot a person like me and still more to my peers. Warm regards; from all of us.
Jordan Travis Scott
bape hoodie comments at 2023-05-27 19:05:41
I simply needed to appreciate you again. I do not know what I would've used without these strategies provided by you concerning such a question. It truly was a very daunting concern for me personally, but understanding the very well-written style you resolved it forced me to jump with joy. Extremely happier for your information as well as trust you know what a great job you were doing training others through a web site. Probably you haven't encountered all of us.
bape hoodie
bape shirt comments at 2023-05-28 21:28:43
I wish to express my appreciation to this writer just for rescuing me from this particular challenge. After searching throughout the internet and finding concepts which were not productive, I believed my life was well over. Existing without the presence of answers to the problems you have fixed as a result of your entire site is a crucial case, and the ones which could have adversely affected my entire career if I had not come across your website. Your own personal knowledge and kindness in maneuvering every part was excellent. I don't know what I would have done if I had not come across such a point like this. I am able to at this moment look ahead to my future. Thanks so much for the skilled and result oriented help. I will not think twice to suggest your web page to any person who should have care about this topic.
bape shirt
jordan sneakers comments at 2023-05-29 15:01:46
Thank you for your whole effort on this web site. Kate loves conducting research and it's easy to see why. Almost all learn all about the powerful mode you render priceless tips and hints by means of the website and therefore cause participation from website visitors on that concept so our favorite princess has been starting to learn a lot. Enjoy the rest of the new year. You have been carrying out a great job.
jordan sneakers
jordan shoes comments at 2023-05-29 23:07:41
I precisely had to thank you very much all over again. I'm not certain the things that I would've used in the absence of the entire aspects shared by you concerning such theme. It was actually a very difficult dilemma in my circumstances, but being able to see your well-written tactic you solved that made me to leap with contentment. I am just happy for your information and as well , have high hopes you know what a powerful job you were undertaking training other individuals by way of your web site. I know that you've never met any of us.
jordan shoes
jordan shoes comments at 2023-05-30 23:11:44
Thanks a lot for giving everyone an extraordinarily splendid chance to read from this website. It really is so fantastic plus jam-packed with a lot of fun for me and my office peers to visit your website on the least three times per week to find out the fresh guidance you have. And of course, I'm at all times satisfied with your eye-popping secrets served by you. Selected 1 facts on this page are in reality the simplest we have all ever had.
jordan shoes
bape outlet comments at 2023-05-31 22:35:37
I must express appreciation to this writer for bailing me out of this incident. Because of scouting throughout the the net and obtaining basics which were not helpful, I believed my life was done. Being alive minus the strategies to the issues you have sorted out through this site is a critical case, and the ones which might have adversely affected my entire career if I hadn't come across the blog. Your know-how and kindness in maneuvering the whole thing was helpful. I'm not sure what I would've done if I had not come across such a subject like this. I can at this time look forward to my future. Thanks very much for the professional and results-oriented help. I will not be reluctant to recommend your web blog to anybody who ought to have tips about this issue.
bape outlet
supreme hoodie comments at 2023-06-01 23:34:24
I as well as my guys were actually reviewing the best helpful hints located on your web page then suddenly I got a terrible suspicion I never expressed respect to you for those strategies. The guys came for this reason glad to read them and now have clearly been loving them. Thanks for turning out to be really kind and for deciding on variety of notable things millions of individuals are really eager to be aware of. My very own sincere regret for not expressing gratitude to earlier.
supreme hoodie
goyard comments at 2023-06-02 17:00:05
I must voice my gratitude for your generosity supporting those people who require guidance on this particular idea. Your personal commitment to getting the solution all-around came to be extraordinarily helpful and have all the time encouraged men and women just like me to realize their ambitions. This helpful recommendations means a great deal a person like me and further more to my colleagues. Many thanks; from everyone of us.
goyard
kd 12 comments at 2023-06-03 00:50:53
I would like to express my respect for your generosity in support of individuals who really need assistance with your niche. Your very own dedication to getting the solution along has been definitely informative and have constantly helped women much like me to arrive at their pursuits. Your own invaluable tips and hints denotes a great deal a person like me and further more to my office workers. With thanks; from all of us.
kd 12
russell westbrook shoes comments at 2023-06-04 02:54:00
I definitely wanted to make a small note in order to thank you for the marvelous advice you are writing on this website. My considerable internet lookup has at the end been compensated with reasonable strategies to share with my great friends. I 'd declare that most of us site visitors actually are extremely blessed to dwell in a very good community with so many outstanding professionals with very beneficial tips and hints. I feel pretty privileged to have seen the webpages and look forward to really more entertaining minutes reading here. Thanks once again for everything.
russell westbrook shoes
ggdb shoes comments at 2023-06-04 17:26:42
I needed to write you one very small word to be able to give many thanks over again on the marvelous information you've provided here. It is quite incredibly open-handed of you to make extensively exactly what many of us might have marketed for an electronic book to help make some dough for themselves, and in particular given that you might well have tried it if you ever wanted. Those basics as well served to be the great way to be certain that other people have similar keenness much like my very own to understand significantly more regarding this condition. I believe there are several more enjoyable occasions up front for many who browse through your blog post.
ggdb shoes
goyard store comments at 2023-06-04 21:33:39
I simply wanted to send a small comment so as to express gratitude to you for some of the unique ideas you are posting here. My rather long internet look up has finally been compensated with incredibly good knowledge to share with my two friends. I 'd tell you that most of us site visitors are very much lucky to live in a notable network with so many wonderful professionals with good suggestions. I feel really happy to have come across the webpages and look forward to tons of more brilliant moments reading here. Thanks a lot again for everything.
goyard store
gap yeezy comments at 2023-06-05 04:53:28
Thanks for your entire work on this blog. Kate delights in making time for investigation and it's really easy to see why. My partner and i hear all of the dynamic way you deliver reliable techniques through your website and therefore foster response from other people about this point then our own child has always been learning so much. Take advantage of the rest of the new year. You are conducting a really great job.
gap yeezy
off white outlet comments at 2023-06-05 23:26:15
I wish to show my thanks to this writer for bailing me out of this type of instance. Just after looking out through the world wide web and meeting advice which are not pleasant, I believed my life was over. Living without the presence of answers to the problems you've sorted out through your main article is a crucial case, as well as those which might have badly damaged my career if I had not noticed the website. Your main know-how and kindness in playing with the whole lot was excellent. I don't know what I would've done if I hadn't come across such a solution like this. I'm able to at this point look forward to my future. Thanks a lot very much for the expert and result oriented guide. I won't be reluctant to endorse the sites to any individual who needs guidelines on this matter.
off white outlet
authentic jordans comments at 2023-06-06 07:08:32
I precisely had to say thanks once more. I'm not certain the things that I could possibly have followed in the absence of those basics revealed by you about my topic. It had been an absolute frightful problem in my view, however , finding out the very professional avenue you handled the issue made me to leap with fulfillment. I will be happy for the information and even have high hopes you realize what a powerful job you are always providing training some other people by way of your website. I am sure you've never come across any of us.
authentic jordans
off white jordan comments at 2023-06-08 03:57:01
I simply needed to say thanks all over again. I am not sure what I could possibly have created in the absence of the information provided by you concerning my problem. It was actually a real hard problem in my circumstances, but being able to see your well-written tactic you handled the issue took me to leap with happiness. I'm thankful for the assistance and in addition hope you find out what an amazing job you're carrying out teaching people with the aid of your blog post. Probably you have never got to know any of us.
off white jordan
supreme clothing comments at 2023-06-08 12:58:00
I really wanted to post a brief remark so as to express gratitude to you for some of the fabulous pointers you are posting at this website. My prolonged internet look up has at the end been paid with sensible know-how to share with my company. I 'd point out that most of us website visitors are unequivocally lucky to exist in a notable website with many awesome professionals with useful advice. I feel very much fortunate to have come across your web pages and look forward to some more entertaining minutes reading here. Thanks once more for a lot of things.
supreme clothing
yeezy boost 350 comments at 2023-06-09 17:24:42
I intended to send you one bit of remark to finally give thanks as before over the remarkable secrets you've featured at this time. It's really wonderfully generous with people like you to present without restraint what exactly most of us would've sold for an ebook in order to make some bucks for their own end, notably seeing that you could have tried it if you considered necessary. These suggestions additionally worked to provide a good way to fully grasp many people have the identical desire really like my own to realize great deal more in regard to this problem. I'm sure there are many more enjoyable times up front for folks who read your blog post.
yeezy boost 350
yeezy boost comments at 2023-06-10 12:02:16
I am also commenting to let you know what a cool discovery my friend's child went through checking your web page. She mastered too many pieces, most notably what it is like to have an awesome coaching style to let other individuals completely have an understanding of selected tricky things. You really surpassed visitors' expectations. Thank you for displaying those priceless, healthy, edifying and as well as easy guidance on this topic to Sandra.
yeezy boost
goyard comments at 2023-06-11 16:21:07
I needed to create you this little bit of word in order to give thanks as before on your fantastic advice you've shared above. It has been particularly open-handed with you to make openly all that most of us could have distributed as an e-book to get some money on their own, primarily given that you could possibly have tried it if you ever desired. Those guidelines also acted as the fantastic way to be sure that other people have the identical zeal just as my own to find out good deal more in terms of this condition. I am certain there are several more pleasurable situations in the future for folks who read your blog post.
goyard
kd shoes comments at 2023-06-12 19:53:17
Needed to post you this bit of remark to help thank you very much over again with your splendid views you have provided on this website. This is really wonderfully open-handed of people like you to allow openly precisely what many people could have offered as an ebook to earn some profit for themselves, precisely given that you could have tried it if you decided. The good tips likewise served to become easy way to be certain that someone else have similar interest much like mine to know the truth great deal more pertaining to this matter. I believe there are many more enjoyable moments in the future for individuals who find out your site.
kd shoes
fear of god hoodie comments at 2023-06-13 04:02:48
I and also my pals were actually checking out the good ideas from your website while at once I got an awful suspicion I never expressed respect to the site owner for them. Those people had been consequently stimulated to see all of them and have definitely been making the most of them. Many thanks for genuinely really accommodating and also for opting for these kinds of helpful themes millions of individuals are really needing to be aware of. Our sincere regret for not saying thanks to sooner.
fear of god hoodie
yeezy boost 350 v2 comments at 2023-06-14 07:14:42
I simply wanted to say thanks once more. I do not know the things that I might have sorted out without the type of solutions documented by you over that question. This was the frustrating scenario in my position, however , noticing the expert technique you handled the issue made me to weep for contentment. I am just happier for this support and in addition believe you are aware of a great job you are always carrying out educating people via a blog. I am certain you haven't got to know all of us.
yeezy boost 350 v2
hermes belt comments at 2023-06-15 02:20:02
I have to express some appreciation to you just for rescuing me from this particular scenario. Just after exploring throughout the world wide web and meeting tricks that were not beneficial, I figured my life was gone. Living minus the solutions to the problems you have fixed all through this write-up is a critical case, and ones that would have adversely affected my entire career if I hadn't noticed your blog post. Your actual training and kindness in taking care of the whole thing was crucial. I'm not sure what I would've done if I hadn't discovered such a thing like this. I am able to now look forward to my future. Thanks a lot very much for the expert and effective guide. I will not be reluctant to endorse the blog to any individual who should get care on this issue.
hermes belt
kyrie 9 comments at 2023-06-15 10:59:51
I wanted to put you this bit of note so as to give thanks over again for your personal splendid techniques you have contributed here. This has been simply pretty open-handed with people like you to convey freely all a number of us could have marketed for an ebook to help with making some bucks on their own, mostly considering that you might have done it in case you decided. These tactics additionally worked as the fantastic way to fully grasp other individuals have a similar eagerness really like my personal own to know way more in respect of this issue. I believe there are several more fun opportunities in the future for those who scan your website.
kyrie 9
air jordan comments at 2023-06-17 09:45:33
I simply wanted to appreciate you once again. I do not know the things that I might have sorted out without the type of information documented by you over this area of interest. Certainly was a hard crisis for me, however , taking a look at the skilled form you processed that forced me to weep over delight. Now i am happy for this assistance and even expect you know what a great job your are undertaking training the others all through your webblog. Most likely you have never come across any of us.
air jordan
fear of god essentials comments at 2023-06-17 19:33:43
I simply wanted to thank you very much again. I am not sure the things that I would've used in the absence of the points provided by you concerning this field. It became an absolute fearsome issue in my circumstances, but looking at the very professional technique you managed it forced me to cry for happiness. I'm thankful for the information and as well , wish you find out what a great job you're providing educating other individuals with the aid of your web site. I am certain you've never met any of us.
fear of god essentials
jordan 13 comments at 2023-06-18 22:12:14
I definitely wanted to post a simple remark so as to thank you for those wonderful guides you are posting on this website. My particularly long internet search has at the end been rewarded with excellent information to go over with my company. I 'd express that many of us website visitors actually are very lucky to exist in a remarkable website with very many special individuals with valuable tips and hints. I feel rather privileged to have come across your web page and look forward to plenty of more cool times reading here. Thanks once again for everything.
jordan 13
off white hoodie comments at 2023-06-20 00:15:19
I want to express appreciation to the writer for bailing me out of this particular matter. Because of surfing through the the net and meeting strategies which were not productive, I was thinking my entire life was over. Existing minus the strategies to the issues you've fixed by means of this blog post is a crucial case, and the kind that might have adversely affected my entire career if I hadn't encountered your web blog. Your personal capability and kindness in taking care of everything was tremendous. I am not sure what I would've done if I had not come across such a thing like this. I am able to at this time look forward to my future. Thank you very much for this specialized and results-oriented guide. I will not think twice to endorse your web site to any person who should have support on this situation.
off white hoodie
gap yeezy comments at 2023-06-21 01:46:59
I intended to compose you the little bit of remark to help say thanks yet again for the extraordinary tricks you've documented on this website. This has been shockingly open-handed of you to convey freely just what a few people might have offered for sale as an electronic book to make some dough on their own, most importantly considering the fact that you could possibly have tried it if you decided. The concepts in addition acted as the fantastic way to be aware that the rest have a similar zeal just as my very own to find out much more when considering this matter. I am certain there are millions of more pleasurable situations up front for individuals that find out your website.
gap yeezy
andylampert comments at 2023-07-08 20:56:29
dolce gabbana baby girl dress shein trendy outfits tory burch tennis dress new york yankees hat toddlers utah quarters white sox wore shorts miami dolphins bucket hat new era 50
andylampert
mirkurortov comments at 2023-07-13 19:06:28
reebok cleveland browns colt mccoy 12 orange authentic jerseys sale zara paisley maxi dresscinderella birthday dress girlruffle tie dressjumper dress 2020 kvinders sort balleerina skonike air max lunar1 deluxe neroadidas zx flux svart leopard printnike air max 90 lunar jacquard blu air force 1 07 premium noir texas rangers sun hat sizes etsy maxi skirt
mirkurortov
makersfinds comments at 2023-07-15 15:46:21
police eyewearoakley discount siteoakley sutro lite blackladies ray ban sunglasses hm kids dresses adidas superstar white with black stripes junior mens oo9102 holbrook square sunglassesoakley holbrook prizm roadoakley sport performance sunglassesrb3025 aviator gradient night dress for women sexyavery wrap dressganni black seersucker dressladies semi formal dresses cute knitted baby boy hats nyc january 2017miami dolphins military hat zipnew york mets hat lids marylandwashington nationals division champs hat map
makersfinds
massamuscle comments at 2023-07-17 04:08:16
christian louboutin snakeskin heels chargers nfl online air jordan 5 maschio tutti blunike air max 90 ultra moire noir and blancmennns svart sko bootssalomon red shoes spigen iphone 12 tough armor nike san diego chargers 17 philip rivers 2013 light blue limited jersey red sox yellow blue uniformscleveland browns jersey youthmarvel nba jerseyssan francisco 49ers apparel
massamuscle
mygohotels comments at 2023-07-18 19:44:18
louboutin shoes cost 1919 cincinnati reds hat pattern city edition nba 2019 fragment design x travis scott x air jordan 1 retro blaze orange rabbit fur hat cleanest nfl jerseys
mygohotels
techonesolution comments at 2023-07-22 09:05:27
sana safinaz ready to wear 2020 stephen curry 3 shoes white blue dallas mavericks mitchell and ness snapback denim western hat white button down shirt bodysuit black widow key caps
techonesolution
cyberverge comments at 2023-08-22 02:15:11
fairy godmother dress upmars twist mini dressblouses for large busted ladiesflowy sparkly dress how to make baby hat crochet pattern generator kansas city royals safari hat 70 ralph lauren navy blue shortslacoste t shirt outletboohooman body warmerjcpenney long sleeve t shirts high low mother of the bride dresses golden state warriors city edition shortsknicks tie dye shirtcavs sleevesmiami tyler herro jersey
cyberverge
hermes comments at 2023-08-23 06:02:07
Your house is valueble for me. Thanks!?
hermes
golden goose comments at 2023-08-24 05:16:22
Oh my goodness! an amazing article dude. Thank you However I'm experiencing concern with ur rss . Don抰 know why Unable to subscribe to it. Is there anyone getting an identical rss drawback? Anybody who is aware of kindly respond. Thnkx
golden goose
sommarbutik comments at 2023-08-24 23:40:30
new orleans pelicans online polo bear football sweaterbrowns salute to service gearoilers drill bit jerseyjustin fields jersey mens wedding louboutins mini wallet on a chain in signature canvas capitals stanley cup patch womens north face black giletcute western shirtsamerican fighter long sleevet shirt oversize outfit
sommarbutik
hermes birkin comments at 2023-08-25 04:49:45
you have an excellent weblog here! would you wish to make some invite posts on my weblog?
hermes birkin
kyrie spongebob comments at 2023-08-30 12:28:33
This actually answered my drawback, thank you!
kyrie spongebob
hermes handbags comments at 2023-09-01 19:53:44
I抦 impressed, I have to say. Actually rarely do I encounter a blog that抯 each educative and entertaining, and let me tell you, you've hit the nail on the head. Your thought is excellent; the problem is something that not sufficient persons are talking intelligently about. I am very completely happy that I stumbled across this in my search for something regarding this.
hermes handbags
golden goose francy comments at 2023-09-02 03:45:25
I wish to express appreciation to you just for rescuing me from this particular incident. As a result of looking throughout the world-wide-web and obtaining techniques that were not productive, I figured my entire life was done. Living devoid of the solutions to the problems you have solved all through your entire short post is a serious case, as well as the kind that could have in a negative way affected my career if I had not discovered your web site. Your actual capability and kindness in maneuvering almost everything was invaluable. I am not sure what I would have done if I hadn't come across such a point like this. It's possible to now look ahead to my future. Thank you very much for the impressive and result oriented help. I will not think twice to propose your blog to any individual who should receive direction on this subject.
golden goose francy
telosanft comments at 2023-09-03 06:21:17
pandora sparkling snowflake pendant spigen moto g 5g plus nike air jordan 14 black and grey nike dunk high prm sb diamond chinese football kit manufacturers white floral chiffon dress
telosanft
yeezy shoes comments at 2023-09-07 22:44:23
Your house is valueble for me. Thanks!?
yeezy shoes
yeezy outlet comments at 2023-09-08 22:19:12
The following time I read a weblog, I hope that it doesnt disappoint me as a lot as this one. I imply, I know it was my choice to learn, but I actually thought youd have one thing fascinating to say. All I hear is a bunch of whining about something that you might repair if you werent too busy in search of attention.
yeezy outlet
jordans comments at 2023-09-09 21:31:34
When I initially commented I clicked the -Notify me when new feedback are added- checkbox and now each time a comment is added I get four emails with the identical comment. Is there any approach you may remove me from that service? Thanks!
jordans
off white clothing comments at 2023-09-10 19:29:55
You made some first rate factors there. I appeared on the web for the difficulty and found most people will associate with along with your website.
off white clothing
Travis Scott Air Jordan comments at 2023-09-11 16:16:26
A powerful share, I simply given this onto a colleague who was doing a bit analysis on this. And he in actual fact purchased me breakfast because I found it for him.. smile. So let me reword that: Thnx for the deal with! But yeah Thnkx for spending the time to debate this, I feel strongly about it and love studying extra on this topic. If potential, as you change into experience, would you thoughts updating your weblog with more particulars? It is highly useful for me. Massive thumb up for this blog put up!
Travis Scott Air Jordan
kd shoes comments at 2023-09-12 13:10:44
I found your blog site on google and verify a number of of your early posts. Proceed to keep up the very good operate. I just additional up your RSS feed to my MSN Information Reader. Searching for forward to reading more from you in a while!?
kd shoes
kobe shoes comments at 2023-09-14 23:48:20
This really answered my drawback, thanks!
kobe shoes
kyrie irving shoes comments at 2023-09-15 11:49:14
you've an excellent weblog right here! would you wish to make some invite posts on my blog?
kyrie irving shoes
bape comments at 2023-09-16 14:48:50
This actually answered my drawback, thanks!
bape
curry 8 comments at 2023-09-17 02:50:46
Aw, this was a really nice post. In concept I wish to put in writing like this moreover ?taking time and precise effort to make an excellent article?however what can I say?I procrastinate alot and by no means seem to get something done.
curry 8
kyrie 7 comments at 2023-09-17 17:06:51
Your house is valueble for me. Thanks!?
kyrie 7
jordan shoes comments at 2023-09-20 00:23:50
An impressive share, I simply given this onto a colleague who was doing a little bit evaluation on this. And he in reality bought me breakfast because I discovered it for him.. smile. So let me reword that: Thnx for the treat! However yeah Thnkx for spending the time to debate this, I feel strongly about it and love studying extra on this topic. If attainable, as you turn out to be experience, would you mind updating your blog with more details? It's highly helpful for me. Big thumb up for this weblog put up!
jordan shoes
supreme clothing comments at 2023-09-21 18:21:55
Aw, this was a very nice post. In concept I want to put in writing like this moreover ?taking time and actual effort to make a very good article?but what can I say?I procrastinate alot and under no circumstances seem to get one thing done.
supreme clothing
kyrie irving comments at 2023-09-26 16:47:57
Youre so cool! I dont suppose Ive learn anything like this before. So good to search out someone with some original ideas on this subject. realy thanks for beginning this up. this web site is something that is needed on the net, someone with a bit of originality. useful job for bringing something new to the web!
kyrie irving
jordan shoes comments at 2023-09-27 05:01:04
I'm often to running a blog and i actually recognize your content. The article has really peaks my interest. I am going to bookmark your web site and hold checking for new information.
jordan shoes
giannis shoes comments at 2023-09-29 01:05:54
Aw, this was a really nice post. In concept I want to put in writing like this additionally ?taking time and precise effort to make a very good article?but what can I say?I procrastinate alot and by no means appear to get something done.
giannis shoes
curry 6 shoes comments at 2023-09-30 04:02:39
Oh my goodness! an incredible article dude. Thank you Nonetheless I'm experiencing subject with ur rss . Don抰 know why Unable to subscribe to it. Is there anybody getting similar rss downside? Anyone who is aware of kindly respond. Thnkx
curry 6 shoes
kyrie 8 comments at 2023-10-03 04:40:29
WONDERFUL Post.thanks for share..more wait .. ?
kyrie 8
off white hoodie comments at 2023-10-08 16:27:08
I used to be more than happy to search out this net-site.I wished to thanks to your time for this glorious learn!! I definitely enjoying each little bit of it and I've you bookmarked to take a look at new stuff you weblog post.
off white hoodie
efornak comments at 2023-10-11 01:40:32
nike sb blazer mid glacier ice rose gold mk bag avalanche 25th anniversary patch michael kors jet set large leather tote green and white sb dunks ralph lauren navy blazer ladies
efornak
goyard bag comments at 2023-10-12 04:12:59
I'm typically to running a blog and i really admire your content. The article has actually peaks my interest. I am going to bookmark your site and keep checking for brand spanking new information.
goyard bag
het-nus comments at 2023-10-15 01:34:04
penguins adidas practice jerseywentz colts shirtwilliam perry bears jerseycharles tillman throwback jersey waterproof case iphone xsiphone 11 case light upredmi note 8 back cover at 99iphone 12 max case designer cowboys jersey 82 nike air max 90 schwarz wolf grau white damen adidas zx 700 core schwarz white super popnike flyknit lunar 3 white womensadidas yeezy 350 black amsterdam for cheapnike fingertrap air max shoes for sale nike kd 7 negro on negrojordan trainers maschioadidas d lillard 3 herren boost blauog 9s jordans
het-nus
palm angels comments at 2023-10-15 13:31:42
Spot on with this write-up, I actually think this web site wants rather more consideration. I抣l in all probability be once more to read much more, thanks for that info.
palm angels
drwalterp comments at 2023-10-19 04:22:55
2 heart tiffanys necklace pandora thin rings moncler copenhague jacketmatches fashion monclermoncler coutardmoncler jacket cheap mens adidas superstar flux red svart gull new york yankees hats ireland florida lb red bottoms
drwalterp
kyrie irving shoes comments at 2023-10-19 22:31:19
You must participate in a contest for one of the best blogs on the web. I'll recommend this site!
kyrie irving shoes
supreme outlet comments at 2023-10-20 15:04:44
You need to take part in a contest for among the finest blogs on the web. I'll recommend this web site!
supreme outlet
bape hoodie comments at 2023-10-24 19:56:16
There are some attention-grabbing points in time on this article but I don抰 know if I see all of them center to heart. There may be some validity but I will take maintain opinion until I look into it further. Good article , thanks and we want more! Added to FeedBurner as properly
bape hoodie
evecalls comments at 2023-10-31 11:09:00
nike air more uptempo royal bleunike free run 3 azul mujeresnike sb svart jumperjordan schuhe vi daniel jones giants jersey for cheapliverpool fc clothing for cheapnba lakers lebron james for cheapjersey jets for cheap jersey home tottenham for cheap suh nebraska jersey for cheap pandora oval earrings huk short sleeve fishing shirtyves saint laurent t shirt womensstafford classic fit premium performance heavyweighttommy hilfiger original regular fit crew
evecalls
polofutar comments at 2023-11-08 19:58:27
cherry coach walletmk backpack originalbeat crossbody clutch in signature canvas with horse and carriage printmk phone case family tree pandora earrings chicago bulls knit hat new era quality adidas track dress embellished corset dresstory burch poplin dressmayqueen couturefeather trim gown jordan retro 12 where to buy
polofutar
Jacquie comments at 2023-11-15 01:12:13
Сколько измерений у человека
hotelruf comments at 2023-11-17 04:43:13
76ers jersey white bobby hull blackhawks jersey jordan 14 black toe og nike air max classic bw white blue red wings black ice jersey nikelab acg.07.kmtr all green
hotelruf
JiDxgIpaQPqm comments at 2024-03-01 00:53:43
BfmJANiyWvU
JiDxgIpaQPqm comments at 2024-03-01 00:53:47
BfmJANiyWvU
Leave a Comment