The main objective of this investigation is to obtain an optimum value for the flue gas recirculation ratio in a 620 MW-Natural Gas Combined Cycle (NGCC) power plant with a 100% excess air in order to have a composition of the exhaust gas suitable for an effective absorption by amine solutions. To reach this goal, the recirculated flue gas is added to the secondary air (dilution air) used for cooling the turbine. The originality of this work is that the optimum value of a Flue Gas Recirculation (FGR) ratio of 0.42 is obtained from the change of the slope related to the effects of flue gas recirculation ratio on the molar percentage of oxygen in the exhaust gas. Compared to the NGCC power plant without flue gas recirculation, the molar percentage of carbon dioxide in the flue gas increases from 5% to 9.2% and the molar percentage of oxygen decreases from 10.9% to 3.5%. Since energy efficiency is the key parameter of energy conversion systems, the impact of the flue gas recirculation on the different energy inputs and outputs and the overall efficiency of the power plant are also investigated. It is found the positive effects of the flue gas recirculation on the electricity produced by the steam turbine generator (STG) are more important than its cooling effects on the power output of the combustion turbine generator (CTG). The flue gas recirculation has no effects on the water pump of the steam cycle and the increase of energy consumed by the compressor of flue gas is compensated by the decrease of energy consumed by the compressor of fresh air. Based on the Low heating value (LHV) of the natural gas, the flue gas recirculation increases the overall efficiency of the power plant by 1.1% from 57.5% from to 58.2%.
1. Introduction
Global climate change is arguably the most challenging environmental problem the world will be facing in coming decades and centuries. The main source of global warming is the electricity production that generates the largest share of greenhouse gas emissions as 67% of global electricity production comes from burning fossil fuels, mostly coal and natural gas [1] . The Carbon Capture & Storage (CCS) is included as an integral part of all climate change mitigation strategies proposed by the Intergovernmental Panel on Climate Change (IPCC) and International Energy Agency (IEA). CCS is a good and viable option for reducing CO2 emissions because it can be implemented on a large scale. However, the high capital cost is often cited as a key barrier by the potential CCS developers and investors. According to some published data, 70% to 80% of the operating cost of a CCS plant is due to the large amount of energy needed during the capture of CO2 from power generation plants using the available technologies [2] .
Gas-fired power plants with Carbon Capture and Storage (CCS) are expected to play a significant role to reduce carbon dioxide emissions from the power generation sector. Compared to coal or oil-fired CHP plants, CO2 emissions from Natural Gas Combined Cycle (NGCC) technology are about 50% and 30% lower, respectively [3] . Moreover, natural gas (NG) is also preferred to the other heavier fuels because the environmental problems are minimized and the total cost of a Carbon Capture and Storage (CCS) is reduced by avoiding corrosion and other technical problems due to impurities (H2S, SOx, NOx, HCl …) in the captured CO2 [4] . On the other side, in order to keep the temperatures in the gas turbine at permissible levels, the combustor has a typical overall excess air ratio (EAR) in the range 3 - 3.5. As a result, flue gas has a molar percentage of CO2 in flue gas of about 3% - 3.5% [4] . However, for an effective CO2 capture by amine solutions, it is recommended to obtain a molar percentage of CO2 in the flue gas around 10 - 15 [5] . Lower CO2 concentrations in the flue gas require a leaner solvent loading to achieve an adequate “driving force” between the solvent and the flue gas stream for high levels of CO2 capture. But leaner solvent loadings require a higher CO2 removal from the solvent, which will increase the amount of energy utilized in the stripper and the cost of the CO2 capture plant.
The corrosion and degradation of amine solutions caused by the presence of oxygen in the flue gas also cause economic, operational, and environmental problems. Literature review of the laboratory studies and pilot plant scale experiments clearly indicates that these solvents undergo, in presence of oxygen, both oxidative and thermal degradation [6] . According to Chakravarti et al. [7] , oxidative degradation of amine solutions occurs when the flue gases contain a molar concentration of oxygen of about 5%. As a consequence, flue gas from natural gas fired turbines will increase the operating cost of the CO2 capture unit also because they contain higher concentrations of oxygen.
High Flue Gas Recirculation (FGR) ratios are desirable because they increase the CO2 concentration and decrease the O2 concentration in the flue gas to be treated in the absorption unit. However, the combustion process sets a limit due to the corresponding reduction in O2 concentration. Due to the importance of the recirculation rate on the overall performance of the CO2 removal process, combustion studies are required in order to define the optimum achievable recirculation rate. The optimum value of FGR ratio will depend mainly on the properties of the combustible, the amount of excess air used and the turbine mechanical limitations.
The first part of this study is to simulate a Natural Gas Combined Cycle (NGCC) for a production of about 620 MW of electricity using the commercial software Aspen HysysV9.0 and the Soave-Redlich-Kwong (SRK) equation of state. Secondly, in order to reduce the cost of capturing CO2 and minimize technical problems related to oxidative degradation of amine solution, optimum value of the flue gas recirculation ratio will be estimated by investigating the effects of the FGR ratio on the composition of carbon dioxide and oxygen in the flue gas. Based on the Optimum FGR ratio, the final objective of this study is to investigate the impact of flue gas recirculation on the different energy inputs and outputs of the power plant and on its overall efficiency. Based on the results of this investigation, the second part of this work is to simulate both a carbon dioxide absorption plant by amine solution followed by a carbon dioxide compression unit for a future enhanced oil recovery (EOR) project.
2. Methodology
2.1. Description of a Typical Natural Gas Combined Cycle Power Plant
As shown in Figure 1, the simplified NGCC (Natural Gas Combined Cycle) power plant is divided into seven different control volumes: Compressor (K), Combustor (CC), Combustion Turbine Generator (CTG), Steam Turbine Generator (STG), Heat Recovery Steam Generator (HRSG), Condenser (C) and Pump (P).
Following the process flow diagram: 1) Fresh air enters the compressor. 2) It is then compressed to a higher pressure. Upon leaving the compressor, air enters
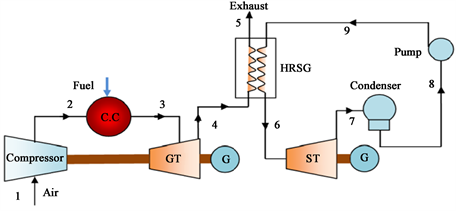
Figure 1. Schematic representation of a natural gas combined cycle [8] .
the combustion system, where natural gas (NG) is injected and combustion occurs. The combustion process occurs essentially at constant pressure. 3) The exhaust gas leaves the combustor and enters the Combustion Turbine Generator (CTG). In the turbine section, the flue gas is expanded to produce electricity. 4) The flue gas leaves the CTG at high temperature. This first part of the power plant is called Open Cycle Gas turbine (OCGT). In the second part of the NGCC, the hot stream from the gas turbine will generate steam in a Heat Recovery Steam Generator (HRSG).The steam cycle consists of a HRSG, Steam Turbine Generator (STG), condenser, and pump to form a Rankine cycle for electricity production. Water enters the HRSG at high pressure and the resulting steam produce electricity in the steam turbine generator (STG). The saturated steam leaving the steam turbine is first condensed and then its pressure increased before returning to the HRSG. The de-aerator of the steam cycle is not included in this investigation.
2.2. Preliminary Calculations
The objective of the preliminary calculations is to determine 1) the amount of natural gas, 2) excess air and 3) the theoretical flue gas recirculation ratio in a natural gas combined cycle (NGCC) power plant in order to produce about 600 MW electricity.
2.2.1. Mass Flowrate of the Natural Gas
Fresh air at ambient temperature is first compressed to 3 MPa then mixed with natural gas (NG) in the combustor of the gas turbine. It is assumed that combustion is complete and all the carbons in NG convert to CO2. The average composition of the available natural gas is presented in Table 1.
For the given mass composition, the average Low Heat Value (LHV) of the natural gas is equal to 46.7 MJ/kg (Aspen Hysys). Based on the LHV, the overall efficiency of NGCC is around 58% [9] . For a power plant producing 600 MW with an overall efficiency of 58%, the needed flow rate of the hydrocarbons of the available natural gas is 22.74 kg/s. The corresponding mass flow rate of the natural gas stream is equal to 23.81 kg/s.

Table 1. Natural gas composition.
2.2.2. Stoichiometric Air
The stoichiometric combustion is a theoretical point in which the optimum amount of oxygen and fuel mix generates the most heat possible and maximum combustion efficiency is achieved. Natural gas mixes with compressed air in the combustor and it is assumed that combustion is complete and all the carbons convert to CO2. The following reactions were used to estimate the theoretical amount of air needed for combustion only:
CH4+(2O2+7.52N2)→CO2+2H2O+7.52N2">






























CH4+(2O2+7.52N2)→CO2+2H2O+7.52N2(1)
C2H6+(3.5O2+13.17N2)→2CO2+3H2O+13.17N2">




































C2H6+(3.5O2+13.17N2)→2CO2+3H2O+13.17N2(2)
C3H8+(5O2+18.81N2)→3CO2+4H2O+18.81N2">


































C3H8+(5O2+18.81N2)→3CO2+4H2O+18.81N2(3)
The AFR (Air Fuel Ratio) was calculated from the mass balance of the atoms of Carbon, Oxygen, Hydrogen and Nitrogen in Equations (1) to (3). Solving the four atomic material balances, the molar stoichiometric AFR (Air Fuel Ratio) is 9.90 and the corresponding mass AFR is 16.91. As a result, 384.53 kg/s. of stoichiometric air need to be added to 23.81 kg/s. of natural gas stream for complete combustion. However, for a turbine using natural gas, 10% of excess air is normally added to the stoichiometric air for combustion [10] . Excess Air (EA) is expressed as a percentage increase over the stoichiometric requirement and is defined as;
EA=ActualAFR−StoichiometricAFRStoichiometricAFR×100%">


















































EA=ActualAFR−StoichiometricAFRStoichiometricAFR×100%(4)
It is sometimes convenient to use the Excess Air Ratio (EAR) defined as:
EAR=ActualAFRStoichiometricAFR">




























EAR=ActualAFRStoichiometricAFR(5)
Using Equation (4) and for 10% excess air, the optimum value of the molar and the mass AFR are 10.89 and 18.60 respectively. The corresponding optimum mass flowrate of primary air for combustion only is 422.98 kg/s.
2.2.3. Optimum Values of Flue Gas Recirculation (FGR) Ratio
As shown in Figure 2, primary air of the gas turbine is the main combustion air. This air is mixed with fuel, and then combusted. Intermediate air is the air injected into the combustion zone. This air completes the reaction processes and

Figure 2. Different air flow paths in gas turbine [11] .
cools down the combustion gases. Dilution air is injected at the end of the combustion chamber to help cool the air to before it reaches the turbine stages. In this study, it is assumed that the primary air (with excess air for combustion) includes both the primary air and intermediate air and the secondary air is the dilution air. The recirculated flue gas is added to the secondary air to be used for cooling the turbine.
A maximum value of the flue recirculation ratio is needed in order to respectively maximize the CO2 concentration and minimize the O2 concentration in the flue gas to be treated in the absorption unit. However, the stability of the flame and the efficiency of the combustion process are also key parameters to consider in order to fix the minimum amount of oxygen needed. For energy-efficient combustion process, the flame is supposed to operate within the stability limits yet with smallest possible fuel consumption. Air entrainment is usually used to provide partially premixed flames. Experiments conducted in a 65 kW combustor operating in a pre-mixed flame mode, indicates that the blow out limit (the point at which a premixed fuel and air mixture is unable to self-sustain) occurs with an oxygen concentration below 13 - 14 vol% [12] . According to ElKady and co-workers, a higher minimum oxygen concentration of 16 - 17 vol% is necessary for good combustion efficiency with acceptable low levels of CO [13] . It should also be noted that unburned methane is a vastly more potent greenhouse gas than carbon dioxide itself, and so gas discharged upstream of its end use adds significantly to the overall climate change impact of the fuel. In this study, Aspen HysysV9.0 and the Soave-Redlich Kwong (SRK) equation of state are first utilized in order to estimate the maximum value of FGR ratio for an excess air varying from 100% to 600%. Based on the preliminary calculations, Table 2 shows the corresponding values of the optimum FGR for EA (Excess Air) changing from 100% to 600%.
For the selected case study of an excess air of 100%, the corresponding mass AFR is equal to 33.82. Therefore, the needed amount of air for combustion and cooling is equal to 768.9 kg/s. (422.98 kg/s are used as primary air for combustion and 346.09 kg/s are used as secondary air for cooling.) This value corresponds to an optimum value of FGR ratio of 0.44.The relationship between the optimum FGR ratio and the excess air (EA) values is shown in Figure 3.

Table 2. Optimum values of Flue gas Recirculation (FGR) Ratio for different values of EA.

Figure 3. Effects of excess air (EA) on the optimum value of FGR ratio.
2.3. Simulation of the Effects of FGR Ratio on the Composition of Flue Gas
For an effective absorption by amine solutions, the molar percentage of CO2 in the flue gas should be higher than 10%. In order to reduce technical problems linked to oxidative degradation of amine in the CO2 capture plant, the percentage of O2 in the flue gas should also be lower than 5%.The positive effects of Flue Gas Recirculation (FGR) on the composition the flue gas have also been investigated [2] [5] [12] [14] Akram et al. [5] studied the effects of recirculating part of flue gas in a 100 KW (plus 150 KW hot water) CHP gas turbine TurbecT100. Their preliminary results indicate that a recirculation ratio of 0.45 increased the molar percentage of CO2 from 1.5% to 3.0% and the molar percentage of O2 decreased from 18.2% to 16.0%. Their results show also that recycling part of the flue gas decreases NOx emissions by decreasing the flame temperature. Using a natural gas-fired power plant of 700 MW, the results presented by Bolland and Saether [2] show that, using a recirculation ratio of 0.4, the molar percentage of CO2 increased from 3.3% to 5.5% and the molar percentage of O2 decreased from 13.8% to 9.8%. To maintain high cycle efficiency, flue gas was cooled before reinjection in the combustor. Abu Zahra [14] used Aspen plus and the Peng-Robinson equation of state, to simulate the effect of flue gas recirculation in an IGCC power plant using a low-pressure gasifier. With all the other parameters of the gas turbine constant, the results indicated that the concentration of CO2 increased from 7.3 (% mol.) to 14.0 (% mol.) with the increase of the flue gas recirculation ratio from 0% to 45%. Moreover, the concentration of O2 decreased from 14.2 (% mol.) to 8.0 (% mol.) with the same increase of flue gas recirculation. This part of this investigation is to simulate the impact of flue gas recirculation ratio on its composition for a gas turbine with an excess air (EA) of 100%. First, the simulation results of the molar percentage of CO2in the flue gas are shown in Figure 4.
As shown in Figure 4, The Flue gas recirculation increases the molar percentage of carbon dioxide in the flue gas entering the absorption unit from 5.8 (FGR = 0.1) to 11.0 (FGR = 0.53). However, from a value of FGR ratio equal to 0.5, the
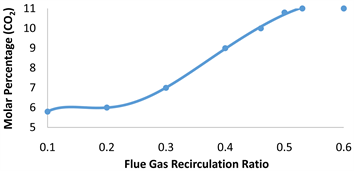
Figure 4. Effects of FGRRatio on the content of CO2 in the flue gas.
molar percentage of carbon dioxide stays constant. This observation could indicate that there is not enough oxygen for the combustion process and carbon monoxide is being formed instead of carbon dioxide. This could also be explained by the fact that the simulated mass flow rate of fresh air (361.1 kg/s) is lower than the minimum needed stoichiometric value of 384.53 kg/s. The optimum value of the flue gas recirculation ratio should therefore be lower than 0.50. Secondly, the effects of the flue gas recirculation (FGR) ratio on the concentration of O2 of the flue gas entering the absorption unit are shown in Figure 5.
As expected, the flue gas recirculation decreases the molar percentage of oxygen in the stream entering the absorption unit from 9.4 (FGR = 0.1) to 0.0 (FGR = 0.53). However, the slope of curve for the values of FGR ratio above 0.42 is larger than the slope of the part of the curve for value of FGR ratio lower than 0.42. This value is selected in this study as the optimum FGR ratio. The corresponding excess air in the primary air is 17% and the molar composition of oxygen in the mix natural gas-primary air is 0.19. This molar composition of oxygen in the gas ?air mixture is higher than the value of 0.17 given in the literature as the minimum concentration for the stability of the flame [13] . In practice, good efficiency of the combustion could be obtained by controlling oxygen and carbon monoxide content in the exhaust gas. For example, the measured CO concentration can be used for combustion control by two methods: controlling O2 when the O2 concentration exceeds a prescribed value and overriding to CO control when the O2 concentration falls below the value, or giving a CO concentration bias (compensation) to the O2 concentration (Figure 6).
Connect to Part II